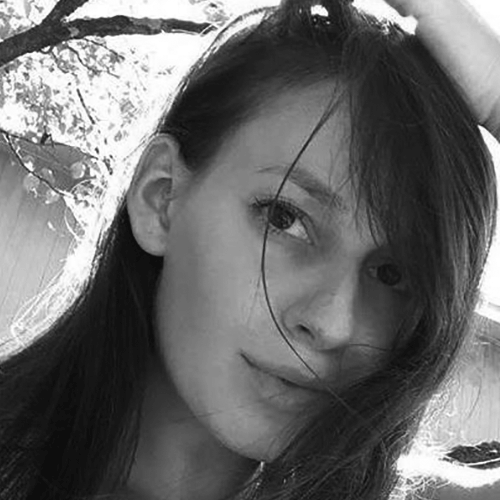
Emily Friedman
Head of Content and Lead Writer at BrainXchange, Lead Journalist and Senior Editor of the EnterpriseWear Blog, and Head of Marketing and Communications for AWE USA and AWE EU
Industry 4.0 presents an opportunity for businesses to diversify their workforces by empowering women and minorities to learn the skills necessary to perform the jobs of tomorrow. Emily Friedman of BrainXchange offers her insights into what companies can do to get the most out of the digital transformation.
Diversity and inclusion is such a hot topic across all industry verticals. What is different about this subject in regards to manufacturing professionals at the current moment?
Diversity and inclusion are notorious issues in the tech world and across C-suites in all industries. The problem extends to the industrial workforce, as well.
Let’s consider women, who made up only 29 percent of the manufacturing workforce in 2016. Manufacturing is a historically male-dominated industry that is increasingly feeling the impact of an aging workforce and skilled labor gap. As the labor shortage reaches crisis proportions, manufacturers cannot afford to ignore half of the population. Persisting barriers to women in manufacturing, whether social or systemic (recruitment programs, employment policies, the workplace itself), therefore threaten the growth and productivity of the industry.
With Industry 4.0, there’s a lot of attention paid to the potential for emerging technologies to empower the workforce, to make existing workers more efficient, productive, and safer. I hear a lot less about the potential for emerging tech to reduce barriers of entry for women in manufacturing or to attract younger and more diverse talent to fill out the manufacturing workforce.
How can women and young professionals best educate themselves on the skills and experience needed to truly impact the modern workforce?
I don’t believe it falls on women or young professionals to prepare themselves for the modern workforce. Our education system should be reckoning with and modernizing in relation to the skills and tools workers will need and use in the future; as should employers.
As a millennial, it’s frightening to think that learning a skill today doesn’t get one as far as it did 50 years ago. Change happens so fast due to technological advancement, evolving business models, shorter product cycles, etc., that 65 percent of the jobs that Gen Z will have to fill don’t even exist yet!
So I think it’s up to the education system and employers to prepare for a future where workers are going to need to be able to learn new skills on command and regularly retrain to remain employable.
What advice would you give to businesses in order to best promote equality and education in the workplace? Is there any specific technology that better enables these types of trainings?
Invest in immersive technology. Now.
One of the strongest use cases of augmented and virtual reality is job training. Knowledge is power and education is the great equalizer, right? (Or something like that.) Some of the world’s largest employers are already using augmented and virtual reality for training (e.g., Walmart) because it works. Compared to traditional methods, training in immersive environments is more effective — trainees learn faster and retain information for longer, without the logistical issues or, in many cases, the dangers of real-life training. Studies from Harvard, Stanford, and other institutions back this up, finding that immersive technology can indeed impart new skills (including soft skills) and change behavior.
Think about it: In VR, you can simulate an infinite number of lifelike simulations to teach anyone anything — anytime, anywhere — from how to repair an airplane engine to how to deescalate a negative customer situation, and even inspect a wind turbine from several hundred feet in the air.
There is so much information out there about so many different aspects of Industry 4.0. What is one thing our readers should remember about this new revolution, and what is one myth you’d like to debunk for them?
Well, for one, robots aren’t going to replace the entire human workforce but advancements in robotics are going to change the nature of work. Automation and robots are already taking over the more menial, repetitive, and dangerous tasks, not replacing workers but freeing them up for new jobs requiring skills that robots can’t yet match (e.g., human adaptability and innovation).
We’re not facing a lack of jobs for humans, but a growing skills gap that’s making fast and effective job training increasingly critical to business. Companies must focus on widening the talent pool, reassessing job qualifications, and investing in technology that will empower the human workforce like augmented reality glasses (for super-human access to information and assistance) and exoskeletons (for the strength and protection to work alongside robots).
Staff, [email protected]