The W.M. Keck Center for 3D Innovation located at the University of Texas at El Paso is dedicated to innovative research into Additive Manufacturing (AM), otherwise known as 3D printing. Lluvia Herrera, research assistant at the center, gives Mediaplanet her insight into what she thinks are some problems facing the manufacturing industry today, and what the future might hold.
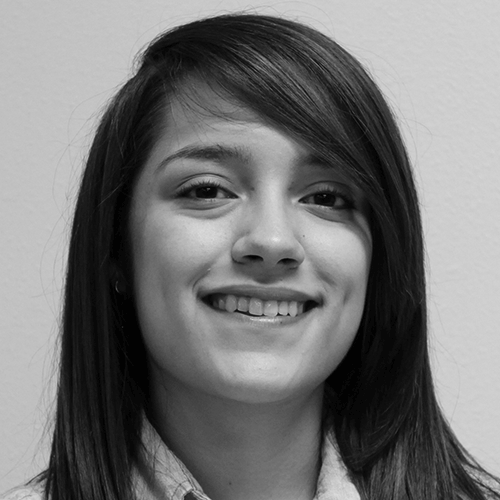
Lluvia Herrera
Research Assistant, The W.M. Keck Center for 3D Innovation
How is your industry benefiting from the renewed focus on manufacturing in the United States?
Additive manufacturing is benefiting through the collaboration of major industries to improve the technology involved and uniting projects throughout the nation. By expanding the industry’s networking systems, solutions to projects would be easier to access as well as resources. Technology applications of additive manufacturing are very flexible, therefore it could facilitate production for many companies.
What can we do to bridge the skilled labor gap?
One of the main things that is concerning me with my peers is that some of them don’t have undergraduate research experience, a summer internship, or co-op where they could essentially build on the knowledge they have gained through their academic career. Through the research they get from said opportunities they could gain a set of skills (such as designing, testing and analyzing of data, and coding among many) that are not practiced in class due to the equipment or projects required. Perhaps introducing a class that requires students to do research in a lab as part of our curriculum would give everyone an equal advantage in becoming a beneficial asset to companies.
What innovations in manufacturing are changing the industry?
The introduction of additive manufacturing in industry reduces the amount of time it can take to build a part (whether from a polymer, ceramic or metal, among many other materials) as well as the cost. This technology enables the user to have more freedom with the design of their part as they are able to experiment with complex geometries. It also allows one to expand the possibilities of testing capabilities though materials that keep surfacing throughout the years.
What are the major challenges for manufacturing companies today?
One of the main challenges that companies face is the lack of hands-on experience from students since it requires time and money to train incoming interns or employees. Communication and problem-solving skills are also crucial since a lack of communication could hinder a project, as well as not knowing how to tackle a problem can stall the project even more. Companies now divide projects in a variation of components that are then assigned to teams of engineers to work on — communication and team-working skills are required now to have a solid beneficial result.
How would you advise manufacturers about implementing effective safety strategies?
A practice that manufacturers could have would be having a team meeting where employees could discuss potential hazards or also attend a safety class provided by the manufacturer periodically (every year or so). Also, by providing the standard equipment needed to be inside a production facility could help vastly in case employees forget their own equipment. Labeling machines and tools with a set of instructions for usage as well as potential hazards that could occur while operating would be helpful.