At Toyota Motor North America, Marisol Barrero is a project manager in ergonomics, and she’s helping steer the company’s ambitious efforts to safely implement new technologies into the workforce.
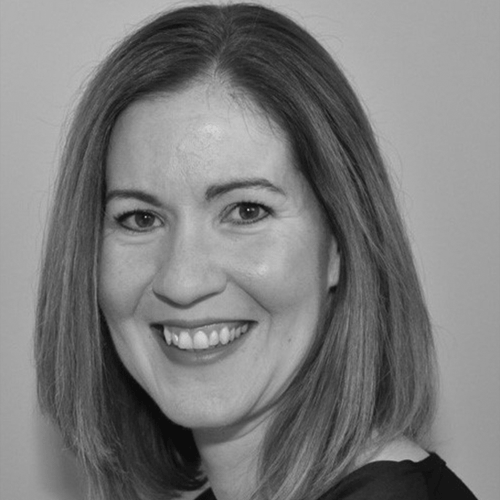
Marisol Barrero
Project Manager, Toyota Motor North America
The automotive industry sees immense benefits from the application of robotics and automation. However, on average, robotics are leveraged for about 1-2 percent of Toyota’s assembly operations. What would you say is Toyota’s philosophy when it comes to manufacturing?
The Toyota Way is always about improving efficiencies but to do it in ways that still allow the team members to add the value that’s necessary in our products, that craftsmanship. We see it as a way to make Toyota better. Our automation ratio today on our assembly lines, where the bulk of our team members work, is no higher than it was 15 years ago and on average, is around 1-2 percent. From a safety perspective, we always aim to eliminate, if possible, and reduce risks from our production jobs. Automation is one way that we can achieve this.
Workplace safety is an ever-growing concern in the manufacturing industry. How are robotics and automation helping to ensure the health and wellbeing of the industrial workforce?
At Toyota, we rigorously follow the hierarchy of controls for risk mitigation. The hierarchy of control involves, in preferred order: elimination, substitution, engineering controls (e.g., a lift assist), administrative controls (e.g., training), and personal protective equipment (e.g., safety glasses). Robotics and automation fall at the top of the hierarchy, so they are most effective at protecting our team members.
How can the integration of automation improve the accuracy of industrial manufacturing tasks?
Exoskeletons:
By using passive exoskeletons, a form of “wearable robotics,” team members can reduce the amount of muscle exertion and fatigue that they would normally experience from their job tasks, such as overhead work, bending, reaching, kneeling, etc. Increased comfort allows more of their attentional resources to be devoted to the work itself, resulting in greater accuracy and quality.
Co-bots:
Collaborative robots, or co-bots, work side-by-side our production team members. They don’t require safety fences because they are light in force and can easily be stopped. They do the type of work that might be more difficult for a production team member. Examples include performing work that isn’t technical in nature, such as picking up a part or applying a piece of mastic across the headliner, or helping when the reach is too far for a team member. They allow production team members to focus on craftsmanship and the fine finesse jobs that are required. We’ve only been using co-bots for about a year and we’re starting to see them in all our facilities. They work beside our production team members but they don’t necessarily work with them. As these robots become more advanced, it will become possible where a robot is doing a portion of the work and you’re actually interacting with them doing a portion of it, and you’re handing off from time to time. The possibilities are unbelievable. The key thing is we always have to have a team member around because they will come up with the ideas for us ways to use them (in the most optimal way).
Toyota New Global Architecture (TNGA) is another example of ways we’re making operations more efficient. TNGA has completely changed the way Toyota makes vehicles. It allows for more flexibility and improves our manufacturing capabilities while enabling us to use same basic components among vehicles on the same platform. Not all about high-tech and robotics, but also human innovation.
The TNGA process for both manufacturing and design will improve lead time. It will also shorten the interval between models that use the common architecture, such as Avalon and Camry. It will improve flexibility so Toyota can respond to market demands quickly as well as improve commonality between processes/plants.
Many in the sphere fear that the widespread adoption of industrial automation will “reduce overhead” by eliminating jobs from the U.S. labor market. Do you believe that is the case?
Not at Toyota. The Toyota Way is always about improving efficiencies, but to do it in ways that still allow the team members to add the value that’s necessary in our products, that craftsmanship. We see it as a way to make Toyota better.
How can automation and robotics improve a company’s bottom line through process and product innovation?
It’s an exciting time to be in the automotive business, as the industry transitions to the future of mobility with automated driving, alternative powertrains, mobility-as-a-service (MaaS), robotics and other technologies on the horizon. As noted, we’re also seeing new opportunities with cobots, where team members can work side by side with robots — even on a moving assembly line.
Part of the emerging conversation in the automotive industry is the development and scalability of autonomous vehicles — what do you think is the future of AV in the next three to five years.
In the next several years, we expect to see Level 4 vehicles, where the automated driving technology can operate in geo-fenced areas under specified conditions, beginning to be deployed. Technology cost remains high, so we expect many Level 4 vehicles will be used in MaaS applications. Service vehicles, which generate income, can amortize the costs much quicker than personally owned vehicles. Toyota’s Guardian approach can be deployed more immediately for personally owned vehicles in the near term. Guardian builds upon the advanced safety technology currently available in vehicles (such as Automatic Emergency Braking, which is standard in nearly every Toyota and Lexus sold in America) by adding sensors and cameras as appropriate to make driving safer. As early as 2020, some of our cars will be equipped with automated driving technology to enable driver-supervised automated driving on highways.