Mining consultant and “Gold Rush” star Dave Turin is often referred to as “Dozer Dave” for his years of experience operating heavy machinery. With an engineering degree and a successful business, Turin has earned his respect in the mining industry. Here’s his advice for creating a successful mining business.
Build partnerships
When it comes to building his team, Turin looks for people with whom he can communicate and work well. “Communication is a two-way street,” he says. “So many times in our industry, we hire people just because they’re a good operator, not because they’re a good person. Personally, I’d rather have a good person on the team. A lot of times I’ll take a young person who is not trained, and then I’ll train them the way I want them to run the equipment.”
Communication is team-wide, so for Turin it’s important to find someone who is a team player. “I believe in teamwork and I love to train our crew as a team, so you need everybody. You need the guy that’s greasing the conveyer and you need the guy that’s running the trucks,” he says.
With the skill shortage confronting the construction industry, Turin emphasizes the importance for businesses to form their own relationships with trade schools. “We stay involved with our schools and our junior colleges,” he says. “When you have kids that have a relationship with the instructors in a trade school, guess who [the instructors] are going to send their best kids to? Right to you.”
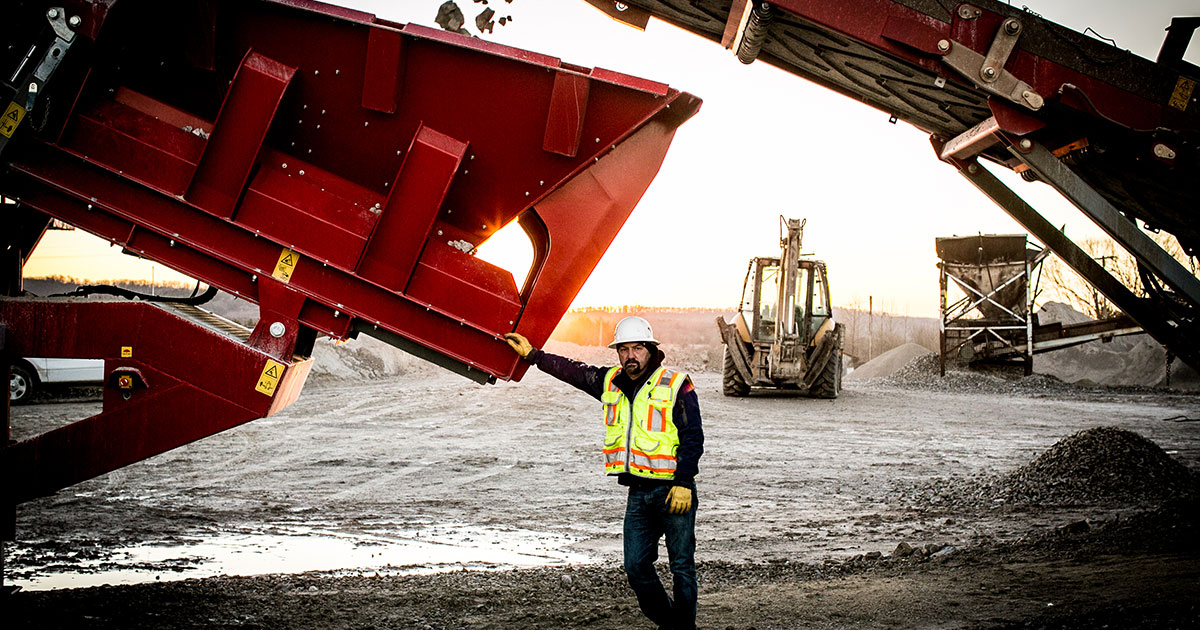
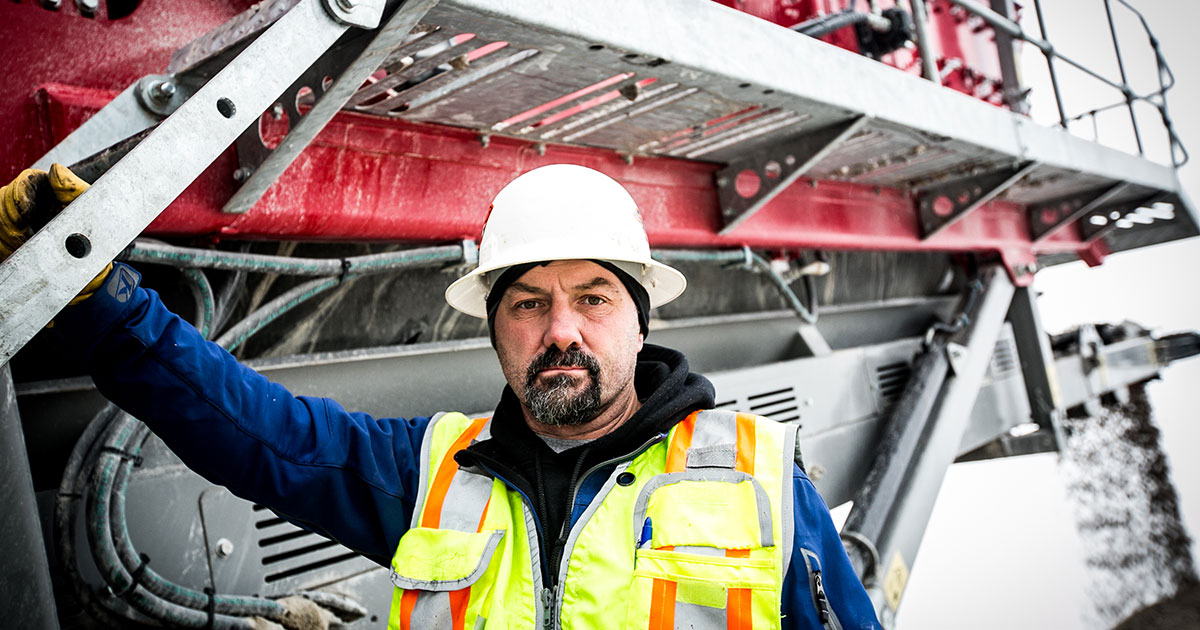
Turin urges us to compare recruitment efforts between athletes and employees as a point of reference. “Look at how much time and effort we put into recruiting college athletes,” he points out. “Really, the college athletes are there for maybe four years. Why aren’t we as businesses recruiting some of those good high school kids?”
When businesses don’t work closely with schools, colleges end up recruiting most of the students. Students are often left not even realizing their other options. “Why don’t we give that same example of how much value we put in an athlete?” asks Turin.
Day-to-day support and interest in a child increases his or her chances of completing school. “If we give a kid a scholarship for a community school — it’s not much — if we spent that and we check up on them every quarter, that kid is probably going to finish up, and then we’ve got a good valuable employee who’s going to stick with us,” says Turin.
Safety first
When it comes to safety on the worksite, Turin says, “One of the biggest things is to be aware of your surroundings. Equipment is not forgiving at all. Too many times we become too focused on our machine and doing what’s right in front of us. If you’re so focused that you can’t see what’s going on around you, that’s a scare.”
Continuing education is also critical for making sure your workforce remains aware of safety concerns. “You have to constantly teach yourself. It doesn’t come with age or experience,” Turin says. “You have to continuously be teaching and coaching.”
To support this philosophy, Turin makes sure all his team members understand they have the right to call someone else out for unsafe practices, even a brand-new employee. “It starts with leadership. You’re responsible for him and he’s responsible for you,” he says. The machinery might evolve, but the safety practices do not.
Look ahead
“Our world in construction and mining has become more technical,” says Turin. “When we get into a newer machine, there are a lot of bells and whistles, and it is for the most part a good thing. It makes our machines easier to analyze and easier to troubleshoot.” But with new machinery, some of his older employees are disadvantaged in terms of skillset.
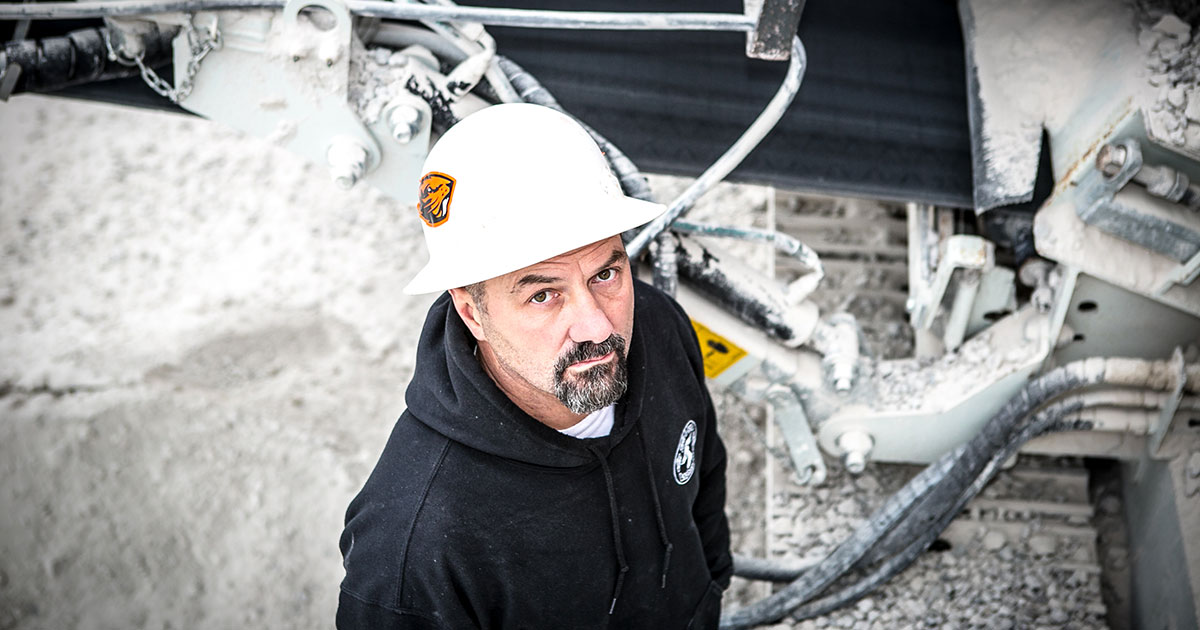
The change hits mechanics and technicians the hardest. “Nowadays, these technicians who come and work on our machines are basically computer guys,” Turin explains. “All of our machines are running on computers, so it takes somebody that knows computers.”
The mechanics, therefore, are becoming more skilled and are getting higher paychecks in return. “They are computer technicians, basically, but they also have to know how to turn a wrench,” says Turin.
“These machines are changing so fast,” he adds. “Our world in the mining and construction industry is becoming so sophisticated and so technical that we need more and more young people.”