Michael Rikkola, the director of analytics at Komatsu Mining, spoke with Mediaplanet about the ways data is accelerating change.
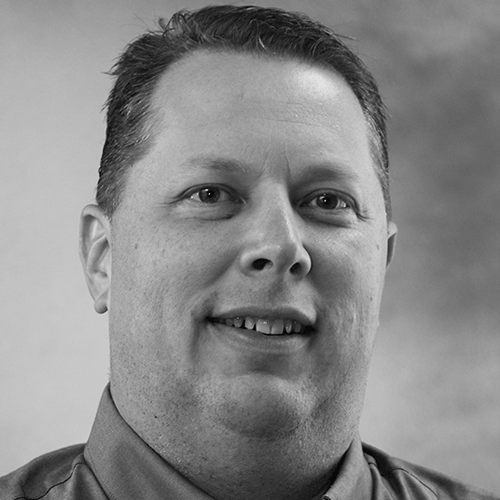
Michael Rikkola
Director of Analytics, Komatsu Mining
What manufacturing innovations are changing the industry?
The promise of autonomous mining has really transformed what had been a historically steel-centric fleet of equipment into a distributed digital mining platform. The proliferation of digital control platforms and sensor technologies on the machines enable growth of data capture and analysis at an exponential rate. The continual advancement of both next-generation networks and autonomous car technologies continue to accelerate change in the industry. At Komatsu, we then feed that operating data to our manufacturing process to shape the future of our product line, increasing the quality of our offerings and enabling smarter products for our customers.
What are some of the energy and cost benefits IoT has on the mining industry?
Modern mining is essentially an ultra-complex optimization problem, with the goal of moving the least amount of waste material as efficiently and sustainably as possible to extract the sought-after minerals. Leveraging IoT allows for optimized loading and haulage management, providing for fewer pieces of equipment that consume significantly less fuel and electricity as previous machines, in addition to lower capital and labor expenses. IoT in mining is enabling just-in-time production of minerals in the same way that lean manufacturing transformed the factory. Smarter, connected equipment and automated processes are allowing mines to optimize mineral blends to increase efficiencies in the manufacturing process, reducing cost and saving energy.
How important are real-time monitoring and data when working on large projects?
Efficient and sustainable mining requires a dynamic operational management model. The saying that one cannot manage what it cannot measure is magnified at mine sites, where it can take up to an hour or more of travel to understand an operational or maintenance condition. The ability to have the right part and right person in the right spot, or make an operational decision across a fleet, has significant impact to operations that measure downtime in tens of thousands of dollars an hour. Every second counts, and we aim to help customers avoid unplanned downtime while safely maintaining production targets.
What is the primary challenge facing the industry, and do we have the resources to address it?
One of the primary challenges of the industry related to IoT is the ability to transform and enrich the terabytes of machine-generated data into definitive, actionable information that improves efficiencies and reduces costs for the mines. There’s a knowledge gap between the traditional big data/IoT solutions and the complexity and uncertainty of mining operations. We are working with customers to encode their traditional mining industry knowledge — combined with Komatsu’s product and engineering understanding — to create next generation IoT solutions that bridge the gap and transform data into information that drives results.
Where do you see the industry in the next 10 to 20 years?
Machines are going to continue getting smarter with more onboard computing. At the same time, machine automation will continue to advance — allowing for the increased use of remote operation. As we continue to grow and improve our ability to turn raw data into information and results, that will help bring together various autonomous projects and capabilities on a mine site, enabling coordinated remote operation and monitoring. This will help remove more people from harm’s way, while optimizing machine performance and mine coordination to enhance safety and production capabilities.