If you know NASCAR, you likely know Brad Keselowski. As one of NASCAR’s top drivers, he’s collected wins at Las Vegas Motor Speedway, among others. But what you might not know about Brad is that he’s a huge fan of manufacturing.
Roots run deep
Brad doesn’t just love manufacturing because it’s one of the key components of his success as a NASCAR driver. It runs in his blood. His grandfather was drafted during WWII but was sent back to Rochester, Michigan, where he drill bits were made for the war because he was skilled machinist, and no one wanted to lose such a precious commodity on the battlefield.
Brad’s father and uncle, too, sparked an interest in both manufacturing and racing, as they were both skilled fabricators. They could, Brad says, build anything on a car. “I watched them build things growing up, and it just amazed me,” he said.
As he got older, Brad began to see a career for himself in racing, inspired by his father, who worked six or seven days a week and then spent weekends racing. “I don’t remember ever NOT wanting to be a race car driver,” he says, “I don’t think I’d be very good at anything else!”
The feedback loop
Manufacturing is essential for Brad’s racing success because he, along with his team of engineers, manufacture their own cars. Teamwork is also critical, because it provides what he calls a “feedback loop.”
“I’m the onboard computer. It’s my job to complain and whine to my team,” he says. When he gives feedback, his team can reengineer and manufacture parts to improve performance based on his input.
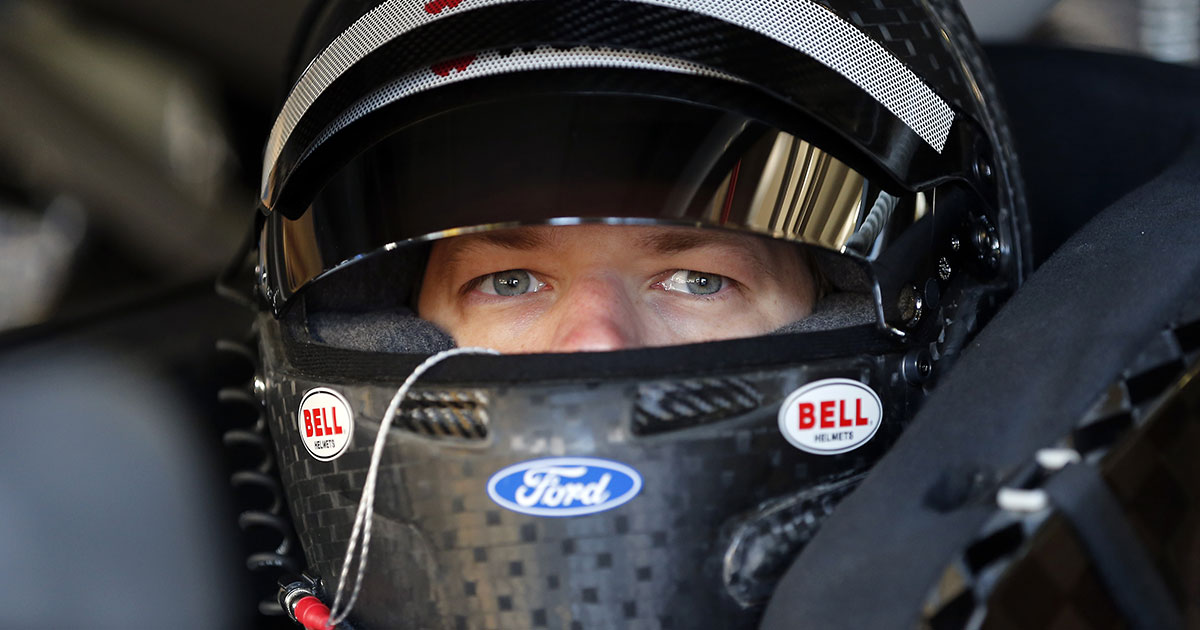
A great example of this feedback loop happened in 2012. Brad and his team were working on a specific part for a car the day before a championship race. During practice, it became clear that they hadn’t properly engineered one part of the rear suspension. With about 14 hours left before the race, time was of the essence.
The engineering team redesigned the part that day, then called the manufacturing facility, who built it that night. The next morning, they flew the part to the race track, bolted in on the car an hour before the race, and ended up winning the championship.
Because that feedback loop was so effective, the team was able to go from problem to utilization in under a day.
Critical factors in manufacturing
From 2007 until 2017, Brad ran his own race team, creating an opportunity to build race vehicles from the ground up. While, ideally, Brad says they would manufacture everything they could, that isn’t usually feasible, so they rely on a number of vendors to supply certain parts.
Looking for the best value with manufacturers and vendors, Brad says there are two essentials: quality and security. “If you have the best part, it’s no longer the best part if everyone has it,” he says. Safety is always a top priority for Brad and his team, especially when it comes to manufacturing custom parts. When they have complete control over the project, they can do things like use molds that fit to the driver’s body. He says that the more the interior of a car is built to his body, the safer it is. “At the end of the day, safety, of course, has to be a priority for a lot of reasons,” he reiterates, “We owe it to each other to protect each other.”
Brad is grateful to the fields of engineering and manufacturing because they have helped him be a success in his industry. He says, “At the core of democracy is capitalism and at the core of capitalism is manufacturing.”