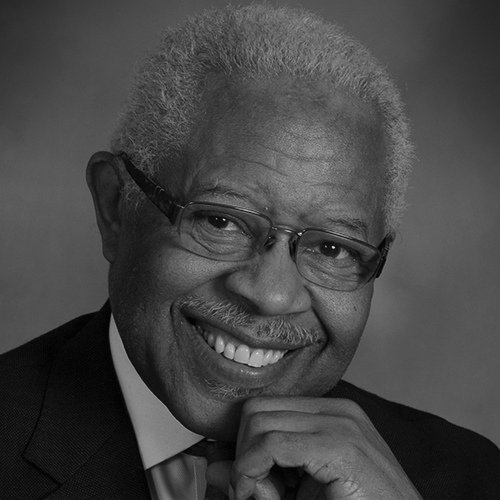
David Burton
Founder and CEO, Diverse Manufacturing Supply Chain Alliance
In the best of times, corporate understanding of need for manufacturing supplier development gets lost in discussions and about “corporate social responsibility,” as detailed in the ISO 26000 standard regarding labor rights, fair operating practices, consumer issues, the environment, human right, and, of course, community involvement and development. But these are not the best of times, and we are faced with three major mega forces that have implications for both large corporations and the manufacturing suppliers in their supply chain network:
- The post-COVID-19 supply chain adjustment and demand for supply chain network resiliency
- The acceleration of supply chain digitization
- Corporate response to the racial inequalities
In truth, diverse supplier manufacturing development is a business imperative far beyond more limited “supplier diversity” discussion. That said, it’s easy to understand why resilience will become the driving force behind the post-Covid-19 recovery. Supply chain disruptions wreaks havoc on continuity of supply business imperatives and their bottom lines. They will make strategic decisions that will have long-term impacts and outlive the pandemic and mitigate future disruption.
The first step in this process will be an examination of supplier content in their supply chain network, consisting of suppliers, warehouses, and distribution channels. Where are domestic supplier with shorter distribution lines? Are they resilient? Do they have creditable and transparent responsiveness, agility, cost, and other key performances? How do I know it? Are they committed to continuous improvement? Can they scale? Is their data safe or so they pose other security risks? The bottom line: are they performance driven, and performance managed with the data that communicates it?
Constituting upwards of 80 percent of the value in supply chain networks, performance alignment and development of supplier capabilities and capacity is central in a large corporation’s recovery strategies. Suppliers that just happen to be diverse must be integral to corporate strategy.
Acceleration of supply chain digitization post-COVID-19 strategies demand commensurate intensification of supply chain digitization. Where pre-COVID-19 supply chains were a series of largely discrete, siloed steps taken through marketing, product development, manufacturing, distribution, and finally into the hands of the customer; digitization brings down those walls where the supply chain network is a completely integrated ecosystem that is fully transparent from the suppliers of raw materials, components, and parts, to the transporters of those supplies and finished goods, and finally to the customers demanding fulfillment.
In a post COVID-19 new normal, there will be a surge of interest in, investment in, and deployment of technologies such as process mining, digital process management, robotic process automation, Internet of Things (IoT), blockchain, cloud, and information management. These data flows will impact the end-to-end supply chain to overhaul outdated processes and mitigate the risk of future market shocks.
I know you’ve heard this a thousand times: “a chain is as strong as its weakest link”. For diverse manufacturing suppliers, that has never been more true.
Why diversity matters
A corporate response to racial inequalities is still a primary source of wealth creation. Diverse manufacturers are more often located in communities in which they create and retain jobs that contribute to economic development. A 2018 skills gap study by Deloitte concludes that Industry 4.0 driven manufacturing operations are creating, “a widening gap between the jobs that need to be filled and the skilled talent pool capable of filling them.” Because manufacturing jobs have a multiplying effect on related employment, opportunity extends beyond the supplier’s four walls into the larger community. Thus, this creates even more jobs and expendable wages that support local economies. There can be no more important tribute to racial inequality issues than economic empowerment.
As a business imperative, diverse supplier development must include buy-in by corporate supplier diversity organizations, sourcing and buying organizations, chief procurement officers and supply chain management, and top corporate leadership. Its real value extends to shareholders interest in long term financial share value. Out of every crisis comes opportunities for competitive repositioning, reinvention, and differentiation. Assessment of the three mega trends can be catalysts for renewed thinking about diverse manufacturing supplier development.