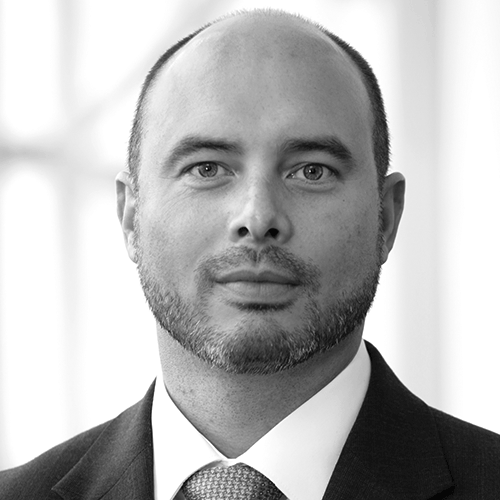
Tim Shinbara
VP & CTO, Association for Manufacturing Technology
Currently, the United States is a leader in developing new and innovative technologies, including artificial intelligence, 3D printing, machine learning, and robotics — all of which have applications in the manufacturing industry. However, the full digitization of manufacturing plants and their connection to each other in a visible, global supply chain will be the development that enables companies to better mitigate disruptions in the future.
The challenges ahead
Various levels of technology adoption and digitization exist in the manufacturing industry today, and larger manufacturers, such as those in the automotive, aerospace, and oil and gas sectors, are further along than smaller and midsized manufacturers (SMMs), which constitute the backbone of the industry. Many SMMs are family owned and have fewer than 50 employees. The industry has been largely self-funded for the past 50 years with businesses earning just enough to reinvest in themselves. While this has led to continuous innovation, it has limited their ability to fully digitize their operations or invest in advanced technologies as rapidly as larger manufacturers. Yet even the largest manufacturers face challenges when creating a fully automated, digitally enabled “factory of the future” that is, in turn, linked to their suppliers around the world.
Collecting data today from the equipment in a manufacturing plant – machine tools, controls, sensors – is relatively inexpensive. However, fully automating a plant requires that all this data be standardized and integrated. This is not trivial. Depending on the size of the plant, there are dozens to potentially thousands of pieces of equipment from multiple vendors that produce their own data. Additionally, data types can differ by the family, make, and model of equipment, as well as the software and versions running on a control.
Think about the challenges white collar industries have faced for the past three decades integrating data, linking PCs to networks, and creating enterprise connectivity and interoperability. On top of this, even the largest companies with the deepest pockets still have silos of critical data locked away in legacy systems such as IBM AS400s, as well as proprietary solutions that are nearly impossible to access quickly or easily. And any gaps in data, standardization, and interoperability limit a continuous thread of automation.
Finally, beyond the individual plant, full interconnectedness across the entire supply chain must be implemented to make it truly visible. A single product may have hundreds of individual components or assemblies, each sourced from dozens of suppliers around the globe. For this global network to operate, all data needs to be accurate, timely, and interchangeable with other factories’ data. Only then will you start to see true supply chain visibility.
Moving forwards
One of the key reasons we recently witnessed so many supply chain disruptions is because of the delayed echo of impact caused by disparate visibility. Hundreds of thousands of individual manufacturing plants around the world are still not adequately connected to even their most critical global suppliers given the lack of data-enabled networks. This is not just a U.S. problem, nor will it be only a U.S.-based solution. A first step is to better equip manufacturers to become more fully digitized and integrated factories of the future.
Such an environment requires all assets in a manufacturing process to be connected, enabling an integrated, seamless flow of data across the value chain, threading together every phase of a product life cycle – from design, sourcing, production, and testing to distribution, point of sale, operation, and service. In conclusion, although this is a pervasive global problem, it is not insurmountable. Standardizing a few key areas of interoperability would significantly increase efficiencies for all manufacturers. A visible supply chain would be one of many practical benefits of digital manufacturing, the digital thread, IIoT, and Industry 4.0 – buzzwords that could, with some effort, help to build a more resilient manufacturing industry.